Die Notwendigkeit zum Beizen von Edelstahl entsteht, wenn die Oberfläche vor dem Korrosionsprozess geschützt werden muss. Als Ergebnis des Ätzverfahrens werden unnötige Oxide und Zunder von der Stahloberfläche entfernt und ein Chromoxidfilm wird gebildet. Richtiges Beizen erhöht die Lebensdauer Ihres Edelstahlprodukts erheblich.
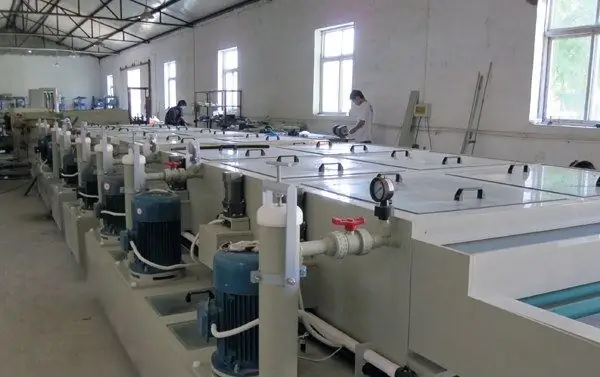
Die Gefahr der Korrosionsentwicklung bei Edelstahl tritt am häufigsten nach dem Schweißen oder nach der mechanischen Bearbeitung des Teils (Schmirgelwerkzeuge, Sandstrahlen usw.) auf. Der Kern des Schadens, den das Metall erleidet, liegt in der Verletzung der Chromoxidschicht, wodurch das Eisen "freigelegt" wird und ungeschützt wird. Daher muss jeder Aufprall auf Edelstahl durch Passivierung, chemisches Ätzen "neutralisiert" werden.
Säurebeizen
Die Verwendung von konzentrierten Chemikalien setzt voraus, dass die Arbeit in einem spezialisierten Raum durchgeführt wird. In der ersten Stufe wird der Kesselsteinabtrag in einem vorbereiteten Bad mit Schwefelsäure (7-8% des Volumens) und Salzsäure (3-4%) organisiert. Der Prozess muss bei einer Temperatur von + 60-80 ° C für 30-40 Minuten durchgeführt werden. Bei der Erstverarbeitung ist die Temperaturkonstanz zu überwachen. Dann werden die Produkte gründlich mit Wasser gewaschen.
In der zweiten Stufe wird das gewaschene Produkt in eine Mischung aus Fluorwasserstoffsäure (1-2 Gew.-%) und Salpetersäure (15-20 Gew.-%) eingetaucht. Abschließend ist eine Spülung mit Wasser erforderlich. Der gesamte Prozess wird von einer starken Freisetzung von Dämpfen begleitet, was auf die Notwendigkeit hinweist, Schutzausrüstung für die Haut und die Atmungsorgane zu verwenden. Das Säureätzen kann von einer Elektrolyse begleitet werden, was die Wirksamkeit des Verfahrens erhöht. Dabei wird ein elektrischer Strom durch das Säuregemisch im Bad geleitet, wobei das zu behandelnde Metall die Rolle einer Anode oder Kathode spielt.
Ätzen mit gebrauchsfertigen Säuremischungen
Nicht jeder Hersteller verfügt über einen eigenen Bereich zum Beizen mit konzentrierter Säure. Daher verwenden viele Menschen fertige Gele, Sprays, Pasten, Konzentrate, die bis zu 4 verschiedene Säuren enthalten können. Zum Auftragen auf die Oberfläche werden säurebeständige Pinsel und spezielle Sprühgeräte verwendet. Wenn Schweißnähte verarbeitet werden sollen, verwenden Sie am besten eine Paste mit dicker Konsistenz - ihre Beizaktivität zeigt sich bereits bei einer Temperatur von + 10 ° C.
Vor Beginn der Behandlung wird das Produkt von Rost, Fett und Schmutz gereinigt. Dazu kann eine spezielle Reinigungsmasse auf die Oberfläche aufgetragen werden, die 30 Minuten einwirken muss. Wenn Gele, Pasten verwendet werden, müssen diese mit einem Griff von 20 cm auf beiden Seiten auf die Nähte aufgetragen werden. Die Dauer der Zusammensetzung beträgt 20-90 Minuten (gemäß Gebrauchsanweisung). Nach dem Spülen wird auf das Produkt ein Passivator aufgetragen, der einen stabilen Chromoxidfilm bildet. Die Haltezeit des Passivators beträgt 30-60 Minuten.